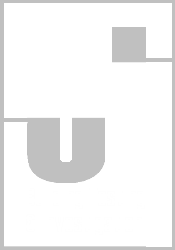
OI is a building envelope testing and moisture investigation firm. We specialize in water infiltration and construction defects in residential, commercial and multi-family structures.
Our testing method takes a very systematic approach to evaluating wall leaks and is applicable to any wall system or material. Other testing firms only conduct tests that are material specific or component specific, and which are basically adaptations of quality control procedures. Forensic evaluation of the building as a whole is absolutely necessary as many times there are multiple intrusion sources.
Testing of fenestrations and exterior cladding is successfully accomplished simulating a wind driven rainfall using a systematic approach. Recreating wind driven rains allows us to accurately identify failure points within the building envelope, when most failures occur.
In addition to building envelope testing, OI performs stucco surveys, infrared evaluations, fenestration & testing audits, CMU (concrete block fill) surveys, expert witness testimony, etc. Our high quality equipment is very portable which makes testing easy anywhere in the continental United States and even easier in the State of Florida.
Tests performed: ASTM E 1105, ASTM E 2128, ASTM E 331, ASTM E 514, ASTM E 547, ASTM E 783, ASTM E 2112, AAMA 501, AAMA 501, AAMA 511
Construction defects cover a broad spectrum from minor problems like popped nails and peeling paint to situations when a house may need to be torn down due to the costs to repair it. Some cases involve leaky walls and/or windows that have led to toxic-mold contamination. Other problems include faulty design, code violations, cracked foundations, substandard workmanship, and unsafe structures. The number of homes with construction-defects has risen in recent years because houses were being constructed in record numbers to meet the high demand for housing. Many general contractors are inexperienced and others mass produce thousands of houses. The home construction industry is intensely competitive. Many builders respond to the competition with low bids for contracts, then cut corners, and frequently employ unskilled or overworked subcontractors and poorly supervise subcontracted work. The combination of these factors results in homes that are built with serious defects.
Construction defects usually include any deficiency in the performing or furnishing of the design, planning, supervision, inspection, construction or observation of construction to any new home or building, where there is a failure to construct the building in a reasonably workmanlike manner and/or the structure fails to perform in the manner that is reasonably intended by the buyer.
Our test method for water penetration of windows, skylights, doors (and roofs, decks, exterior wall, cladding, flashings, and mass wall assemblies) are in general accordance to the ASTM E 1105, E 331, E 2128, AAMA 502, AAMA 503, AAMA 511 standards. The procedure includes water leakage testing along with interviewing the building occupants / owners / tradesmen / contractors, etc, reviewing drawings and specifications (where applicable), surveying the building components, and performing exploratory openings. This test utilizes a spray rack (meets ASTM E 331 & 1105 Calibration tests and AAMA 502-02 requirements) to apply water to the exterior surface of the wall, window, or other test area. Areas to be tested are isolated by systematic positioning of the spray rack and/or by careful masking off the wall components. This moisture test method covers the determination of the water resistance of test site or test area to water penetration when water is applied.
Water testing of fenestrations is applicable for commercial construction, Division 8 required mock-ups.
Building Envelope Testing / Moisture Intrusion Detection (ASTM 2128) OI implements methods for determining and evaluating causes of water leakage through the building envelope. Water penetration (leakage or intrusion) can be problematic if moisture levels exceed the planned resistance or temporary retention and drainage capacity of the wall, is causing or is likely to cause premature deterioration of a building or its contents, or is adversely affecting the performance of other components. Investigative techniques may be intrusive, disruptive or destructive.
Stucco surveys are performed on both residential and commercial properties. Evaluations address common construction deficiencies and components that cause or may cause moisture intrusion related defects. Our firm utilizes various methods and equipment to perform destructive and non-destructive stucco surveys.
Non-Destructive Evaluation: A visual and infrared survey can provide a good indication of water damage to perimeter wall sheathing, framing, and other various areas of the structure. Visual inspections allow us to accurately evaluate subtle signs of water damage, including the appearance of the stucco itself as well as visible characteristics of flashing, grading, and stucco installation. In addition to a visual assessment, we use infrared analysis (thermography) which offers a non-destructive means for assessing the entire building envelope. Moisture found using infrared is then verified using specialty moisture detection equipment found within the structure.
The non-destructive evaluation with moisture survey is the most common type of stucco inspection. However, when water damage is confirmed, more invasive measures may be needed to determine the source of the intrusion.
Inspections with moisture testing, thermography, and destructive or invasive investigation is very common when determining damage and route of problems. A destructive investigation provides a more definitive assessment of potential stucco problems and mechanisms for water intrusion as we are able to identify the moisture migratory path. The lath, stucco, flashings, sheathing, and weather-resistive membrane can also be evaluated to relevant building standards.
Moisture intrusion can devastate a structure as it can foster mold, promotes decay and will often times attract termites. OI utilizes infrared thermography to locate hidden active moisture in building materials. Infrared is often used to help locate moisture intrusion points and to find the water migratory path during testing.
In addition to moisture detection, infrared is used in a multitude of other construction defects such as electrical deficiencies, mechanical maintenance, insulation voids, concrete voids in structural columns, etc.
During our moisture testing, we will perform thermography scans to search for and/or verify moisture intrusion points.
A Cell Fill Evaluation utilizes infrared technology (aka, thermography) to find whether or not concrete reinforcing (grouting) has been properly placed in Concrete Masonry Unit (CMU) or 'block' walls. In order for concrete wall to be structurally sound, the cells need to be filled with grout and rebar pursuant to engineered plans. Infrared allows us to “see” missing areas of grout and identify possible structural failure points using non-destructive methods.